High Precision Injection Molding: Revolutionizing the Manufacturing Industry
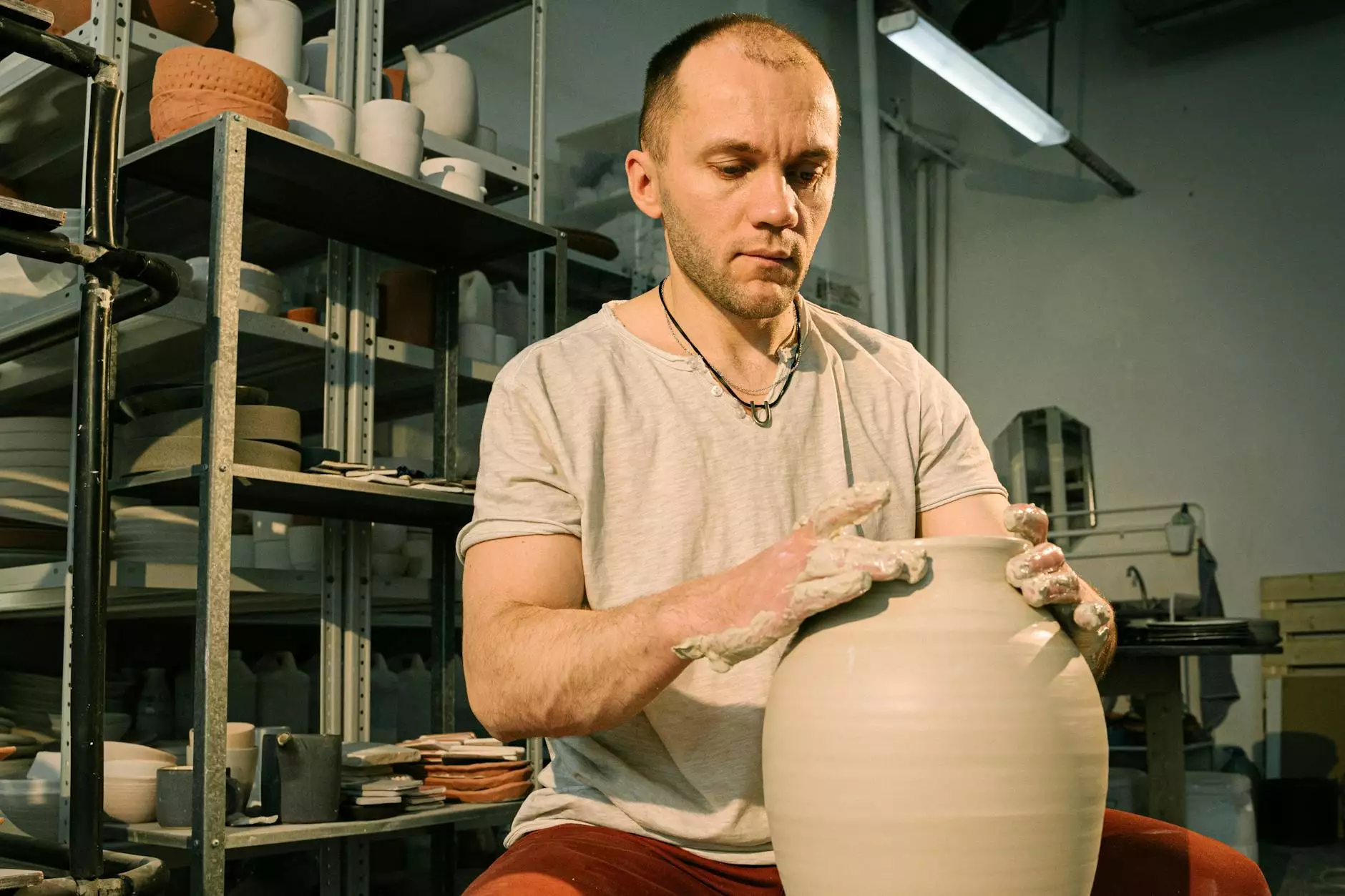
In the contemporary manufacturing landscape, the significance of high precision injection molding cannot be overstated. This advanced manufacturing process is pivotal for industries that demand exceptional product quality, intricate designs, and optimized production timelines. At deepmould.net, we specialize in leveraging this innovative technology to provide unparalleled metal fabrication solutions that meet our clients' evolving needs.
Understanding High Precision Injection Molding
High precision injection molding is the process of creating parts by injecting molten material into a mold. This technique is renowned for its ability to produce complex shapes with tight tolerances. Let's delve deeper into the essentials of this process:
What is Injection Molding?
Injection molding is a manufacturing process that involves:
- Heating thermoplastic or thermosetting polymers until they become molten.
- Injecting the molten material into a mold cavity under high pressure.
- Cooling the material to solidify it into the desired shape.
This method is favored due to its efficiency, consistency, and ability to produce high volumes of parts in a short time frame.
Precision in Manufacturing
The term high precision refers to the strict tolerances that can be maintained throughout the injection molding process. This is achieved through:
- Advanced machinery that monitors and adjusts the injection parameters.
- High-quality molds that are fabric-made with precision-engineering standards.
- Continual testing and quality assurance protocols.
The result is a finished product that meets or exceeds the stringent specifications set forth by various industries, including automotive, medical, and consumer goods.
The Advantages of High Precision Injection Molding
Choosing high precision injection molding offers numerous advantages for manufacturers. Here are the primary benefits:
1. Exceptional Accuracy
One of the most significant benefits of high precision injection molding is its ability to produce parts with incredible accuracy. This is essential for complex applications where every millimeter matters.
2. High Throughput
With the capacity to produce thousands of units in a single production run, injection molding is unparalleled in terms of efficiency. This enables businesses to scale operations quickly and meet market demands without compromising quality.
3. Cost-Effectiveness
Although the initial setup cost for molds can be high, the overall cost per unit decreases significantly with increased production volume, making high precision injection molding an economically viable option for mass production.
4. Reduced Waste
Injection molding is a highly efficient process that minimizes material waste when managed correctly. The precision of the method allows for better material usage, further reducing costs and environmental impact.
5. Versatility in Material Use
This process accommodates a wide variety of materials, including:
- Thermoplastics
- Thermosetting polymers
- Elastomers
This versatility allows manufacturers to tailor product qualities suited for specific applications, such as enhanced durability or flexibility.
Applications of High Precision Injection Molding
The applications for high precision injection molding span numerous industries. Some noteworthy applications include:
1. Automotive Industry
In the automotive sector, injection molding is essential for producing complex components, such as:
- Dashboard parts
- Control panels
- Exterior body panels
The precision and reliability of these components are vital for ensuring vehicle safety and performance.
2. Medical Devices
In the medical field, precision is non-negotiable. High precision injection molding is used to manufacture:
- Syringes
- Diagnostic equipment
- Implantable devices
These applications highlight the importance of stringent quality control and regulatory compliance in medical device manufacturing.
3. Consumer Electronics
The fast-paced world of consumer electronics demands rapid development and high-quality components. Injection molded parts are prevalent in:
- Smartphones
- Laptops
- Wearable technology
High precision injection molding enables these products to achieve sleek designs while maintaining durability and functionality.
Choosing the Right Partner for High Precision Injection Molding
Selecting a capable and reliable partner for your injection molding needs is crucial. Here’s why deepmould.net stands out:
1. Expertise and Experience
With extensive experience in manufacturing high precision injection molded parts, the team at deepmould.net offers valuable insights and innovative solutions tailored to your specific needs.
2. State-of-the-Art Technology
Utilizing the latest in manufacturing technology, we ensure that every part produced meets the highest standards of precision and quality.
3. Customized Solutions
At deepmould.net, we understand that every project is unique. Our team collaborates closely with clients to develop customized solutions that fit their specifications and budget.
4. Commitment to Quality
Our commitment to stringent quality assurance processes guarantees that every product is manufactured to the highest standards, ensuring performance and reliability.
Future Trends in High Precision Injection Molding
The future of high precision injection molding appears optimistic, with several trends shaping its evolution:
1. Sustainable Practices
As industries move towards sustainability, the demand for eco-friendly materials and manufacturing practices is rising. High precision injection molding will increasingly focus on:
- Using recycled materials
- Reducing energy consumption
- Implementing waste reduction strategies
The push for sustainability will likely shape how manufacturers operate in this field.
2. Advancements in Automation
Incorporating automation into the injection molding process can enhance efficiency and reduce the risk of human error. Future advancements may include:
- Robotic arms for part handling
- Smart sensors for real-time monitoring
- Data analytics for process optimization
These innovations will lead to even greater precision and higher production rates.
3. Enhanced Material Technologies
As new materials are developed, the applications for high precision injection molding will expand. Anticipated advancements include:
- Biodegradable plastics
- Advanced composite materials
- High-performance polymers
These materials will drive innovation across multiple industries, enhancing product capabilities.
Conclusion
In conclusion, high precision injection molding is set to play a fundamental role in the future of manufacturing. It offers numerous advantages, from unparalleled accuracy to cost-efficiency, and is essential for producing high-quality components across a broad range of applications. By partnering with experts in the field, such as those at deepmould.net, businesses can stay at the forefront of innovation and quality in their respective industries. Embracing the opportunities provided by this sophisticated manufacturing process can lead to exceptional product performance and competitive advantage.